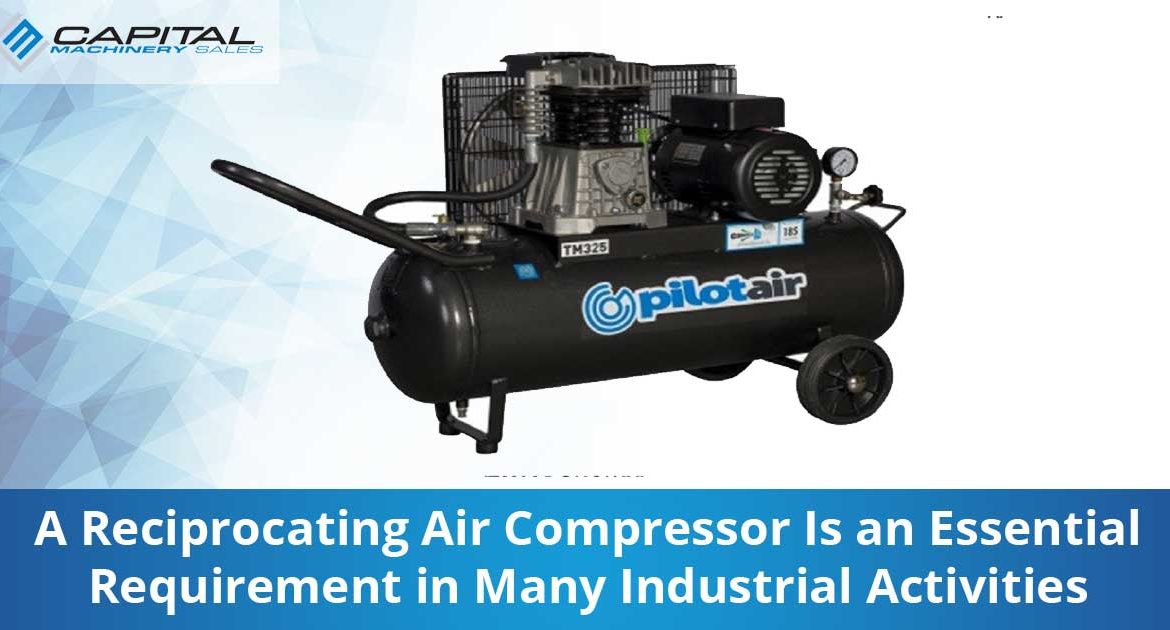
A Reciprocating Air Compressor Is an Essential Requirement in Many Industrial Activities
The objective in using air compressors is to reduce the volume of air which in turn leads to an increase in pressure. This air, which has been pressurized, is then stored in vessels and can be used as required at the point of use, through pipes that have control valves. A reciprocating air compressor is a machine that uses positive displacement to achieve this volume reduction and pressure increase.
Pressurized air is used in a number of industries for various applications, and it is not uncommon for large manufacturing facilities to have a centralized air compression unit which delivers compressed air, wherever it is required within the factory layout. Compressors of the reciprocating type have a very rugged construction and can work for long periods of time, which is why they are largely preferred in industries. Compressors can be single stage or multi stage and both have their own uses as they produce different pressures.
Single stage compressors will have a number of cylinders of the same bore, and pistons compress air against the head of the cylinder to enable the pressure to be raised. The pressurized air is then transferred to storage tanks. These compressors produce medium pressure and can be used for operations like painting, using pneumatic tools, blow molding, filtration etc. Two stage compressors compress the air twice before it is stored. After the first stage, which is similar to single stage compressors, the compressed air which has a raised temperature is sent through a heat exchanger to cool the air, which is then sent to the high pressure cylinder. This cooling increases efficiency of compression. The high pressure cylinder will have a smaller bore, as then the power required for compression remains the same. A reciprocating compressor can have cylinders of the low and high pressure opposite each other, horizontally or vertically.
The operation of reciprocating compressors causes very high vibrations, and that is why it is necessary that the machines have very strong foundations made of reinforced concrete. The vibrations are caused by the twin pistons reciprocating in opposite directions. The need for air pressure is constant and this requires these compressors to be very robust, to be able to stand long hours of non-stop work. Depending on the pressures required, additional compression stages can be added, and this will depend on the industry for which the air is being compressed. You can also buy small units that are portable and are very much in use for cleaning and painting activities.
The working of these compressors does produce a lot of noise and it is not uncommon to have them installed in locations away from normal activities. In certain cases, noise abatement procedures may also be undertaken, like using flexible foundations and sound deadening material or enclosures. Compressors also produce a lot of heat and arrangements have to be made for proper ventilation to allow this heat to dissipate. Tank sizes for the compressed air will depend on the capacity of the compressor, and the use for the air. Pressure drops occur slowly in larger tanks and allow for continuity of operations. Compressed air may also require to be filtered.